Materiali compositi
14/03/2015
Come costruire i tubi in carbonio/kevlar monostrato
Ecco un metodo semplice e collaudato per realizzare tubi in materiali compositi senza l'impiego di stampi.
Se le procedure saranno seguite nei dettagli e di dispone di un minimo di attrezzatura, garantisco un buon risultato.
Scelta dei materiali
E' molto importante scegliere il tipo di tessuto.
In commercio esiste infatti una grande varieta' di materiali adatti alle diverse applicazioni e non tutte sono intercambiabili.
I dettagli tecnici richiederebbero un voluminoso trattato, per cui al momento mi limito all'essenziale. In seguito entreremo nei particolari.
Per questo progetto useremo un tessuto molto sofisticato, formato da due tipi diversi di fibre: carbonio e kevlar.
Fisicamente si presenta come un intreccio di "rovings", fasci di 12.000 fibre elementari raccolte in circa 1,8 mmq di sezione.
La trama e' alternata tra rovings di kevlar (di colore giallo) e carbonio (di colore nero).
Il carbonio ha delle qualita' meccaniche molto particolari: ha un coefficiente di elasticita' ridottissimo, in pratica ha un'ottima resistenza alla trazione e quasi non si allunga sotto sforzo.
In compenso, se piegato in senso longitudinale si spezza facilmente.
Il kevlar e' invece tenace, ha una buona resistenza alla trazione ed e' in grado di sopportare delle forti flessioni senza rompersi.
Basti pensare che e' impiegato nella costruzione dei giubbetti antiproiettile.
L'accoppiata carbonio/kevlar offre percio' le migliori caratteristiche meccaniche di entrambe le fibre:
Una eccezionale rigidita' e un'ottima resistenza alle sollecitazioni.
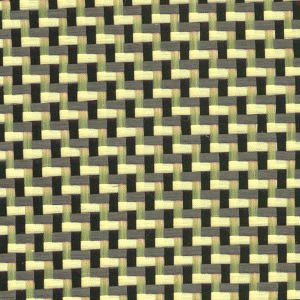
Il tessuto GK210 (distribuito dalla ditta Angeloni di Mestre) e' composto da una trama a 90 gradi di rovings di carbonio e kevlar alternati
Ne risulta un tessuto bidirezionale che resiste ottimamente in entrambe le direzioni di sollecitazione.
Il peso e' di soli 210 grammi al metro quadro.
Per ottenere una simile resistenza usando tessuto in fibra di vetro il peso dovrebbe essere almeno quadruplicato!
Attenzione! I tessuti in carbonio o kevlar richiedono tassativamente la laminazione con resina EPOXY, percio' al momento dell'acquisto non cadete nella tentazione di prendere la resina poliestere, solo perche' costa meno!
Il prezzo della resina epossidica di aggira intorno ai 30 Euro/Kg, contro i 6/7 Euro della resina poliestere.
Prepariamo il formatore
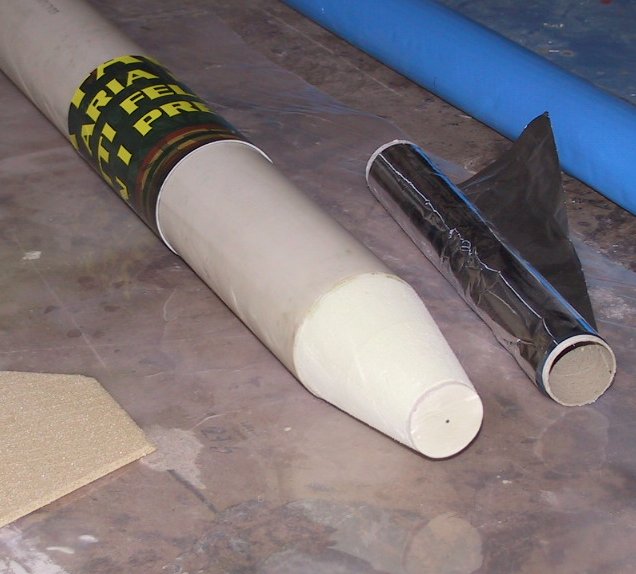
.
Questi tubi sono fabbricati in diametri standard, percio' saremo vincolati a delle dimensioni prestabilite.
Con un tubo da 60 mm otterremo un corpo missile da circa 64 mm, con uno da 80 mm ne otterremo uno da circa 84 mm, mentre con uno da 100 mm ne ricaveremo uno da 104 mm.
Cio' non significa che lo spessore finale del tubo sara' di 2 mm, in realta' questo potrebbe variare da 1mm a 2mm a seconda del numero di strati che stabiliremo.
Lo spessore eccedente e' rappresentato dal materiale di rivestimento impiegato per facilitare l'estrazione del formatore dall'interno del tubo in composito.
Non preoccupiamoci delle ogive e delle transizioni coniche perche' in seguito vedremo come realizzarle con una tecnica similare.
Non e' indispensabile usare un tubo di colore arancione, che pur se robusto e' anche pesante e costoso, e' sufficiente il tipo di colore bianco o grigio.
L'importante e' che sia diritto e regolare, senza deformazioni o imperfezioni.
Per prima cosa tracceremo con un pennarello una linea nel senso della lunghezza e con un seghetto alternativo effettueremo un preciso taglio, ma solo su un lato, in modo che il tubo rimanga unito.
Ora dovremo pulirlo e levigarlo con carta abrasiva fine. I lembi tagliati dovranno essere ricoperti con uno strato di nastro adesivo sottile, ottimo quello per imballaggi.
Alla fine lo lucideremo con il polish per auto.
Prendiamo ora un rotolo di alluminio sottile, di quello usato per conservare generi alimentari e rivestiamo il tubo con uno strato a spirale in modo da ricoprirlo del tutto.
E' possibile fissare l'estremita' del foglio al tubo con un pezzetto di nastro adesivo e poi farlo ruotare avvolgendoci sopra la pellicola, l'importante e' che non si formino grinze o bolle d'aria.
Ripetiamo l'operazione per altre due volte, sovrapponendo la pellicola a quella sottostante.
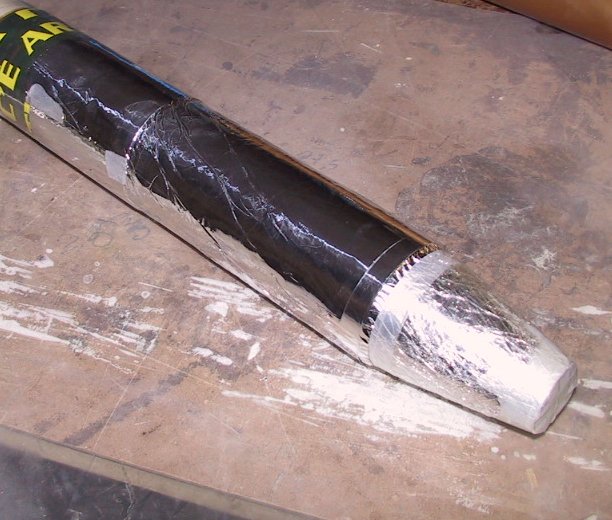
Gli strati di alluminio dovranno ora essere rivestiti da un'altra pellicola, questa volta in polietilene, quel film trasparente usato per conservare i generi alimentari.
Con molta cura ne avvolgeremo altri tre strati sopra il rivestimento di alluminio, facendo molta cura a non formare bolle d'aria.
Un metodo per evitarle e' quello di comprimere il film mentre si avvolge con l'ausilio di un rullo in gomma.
Il risultato finale dev'essere una superficia liscia regolare, senza protuberanze o rugosita'.
Per ultimo tracceremo con un pennarello la linea di mezzeria longitudinale del tubo.
A questo punto possiamo iniziare la laminazione.
Infiliamoci dei guanti di lattice sottile (non servono quelli sterilizzati da chirurgo che costano una follia).
Tagliamo il tessuto necessario a rivestire il tubo con due strati, lungo quanto serve ad arrivare quasi alle estremita' del tubo.
E' importante lasciare qualche centimetro in eccedenza, che verra' tagliato in seguito.
Pesiamo il tessuto con una bilancia di precisione (ottime quelle elettroniche da cucina, con risoluzione di 1 o 2 grammi), da scartare quelle meccaniche in quanto troppo imprecise.
Il peso del tessuto dovra' essere uguale al peso totale della resina da usare per la laminazione, tenendo conto anche degli sfridi.
In realta' il rapporto corretto sarebbe quello di 40% di resina e 60% di tessuto.
Come gia' detto, la resina dovra' essere esclusivamente del tipo EPOXY.
La resina poliestere non e' idonea a questo genere di applicazione perche' non ha buone caratteristiche meccaniche, si ritira con la polimerizzazione in quanto contiene solventi e puzza terribilmente.
Peggio ancora, proprio perche' contiene solventi ha il brutto vizio di attaccare (ed anche sciogliere) le materie plastiche.
In un barattolo pulito mettiamo la quantita' di resina che ci serve, poi ci mettiamo l'induritore nella dovuta proporzione, indicata su ogni confezione di resina.
La quantita' dev'essere assolutamente precisa, altrimenti la catalizzazione non sara' perfetta.
Osserviamo che nella resina epoxy la percentuale di induritore e' molto elevata rispetto alla resina poliestere, circa il 30% contro circa 1 o 2%.
In effetti l'induritore viene incorporato nella massa della resina e non e' un semplice catalizzatore.
Mescoliamo i due componenti con uno stecco il legno o plastica per almeno 3 o 4 minuti, facendo attenzione che TUTTA la resina sia mescolata, compresa quella presente sui bordi e sul fondo.
Si formeranno nella massa delle microbolle d'aria che rendereanno il colore leggermente lattiginoso. Cio' e' normale.
Una perfetta miscelazione e' fondamentale per la buona riuscita della laminazione.
In caso di dubbio meglio mescolare qualche minuto di piu', tanto la lavorabilita' e' abbastanza lunga (dai 40 ai 60 minuti).
Quando la resina e' pronta possiamo inzuppare un frammento di gommapiuma o spugna e la stendiamo abbondantemente sullo stampo precedentemente preparato.
Tutta la superficie dev'essere uniformemente bagnata con la resina.
Per ottenere cio' possiamo ricorrere a qualche trucco, come quello di infilare un manico di scopa dentro il tubo formatore ed appoggiarlo a delle cassette di legno laterali.
In questo modo il tubo e' libero di ruotare per agevolare il nostro lavoro.
Appena la resina e' distribuita sul tubo possiamo applicare l'estremita' del tessuto in prossimita' della linea di mezzeria e la facciamo aderire picchettandoci sopra con la spugnetta inzuppata di resina.
Ruotiamo il tubo lentamente e facciamo aderire il resto del tessuto fino a terminarlo, eventualmente anche in due strati.
Il lembo terminale dovra' sovrapporsi di qualche millimetro a quello sottostante in modo da non creare rigonfiamenti.
Sempre con la spugnetta picchettiamo su tutta la superficie in modo a bagnare uniformemente il tessuto ed eliminare le bolle d'aria.
Il tessuto correttamente inzuppato si riconosce dal colore piu' scuro e dalla sua lucentezza, al contrario un tessuto non sufficientemente impregnato e' piu' opaco e chiaro.
Impieghiamo la resina che ci resta distribuendola sulle parti carenti, fino a terminarla.
A questo punto dobbiamo affrontare la parte piu' delicata di tutto il lavoro, quello di "insaccare" il nostro tubo avvolgendolo nuovamente nella pellicola trasparente, per ottenere in questo modo la superficie piu' liscia e regolare possibile.
L'operazione non e' facile, come minimo occorre essere in due persone, volenterose e disponibili ad imbrattarsi di resina (mi raccomando i guanti di lattice).
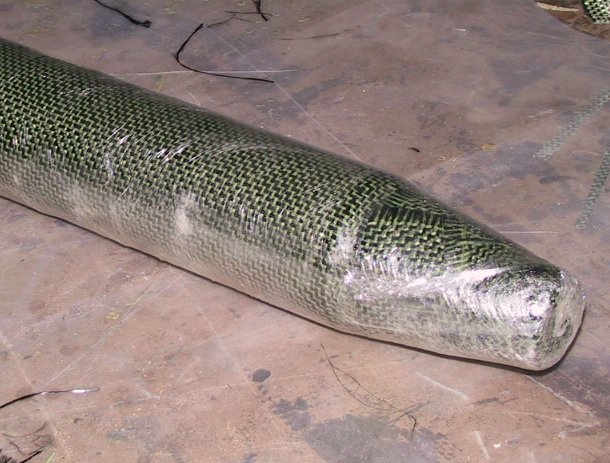
L'avvolgimento va fatto nello stesso verso del tessuto, in modo da comprimere il lembo sovrapposto.
Con molta pazienza e precisione, il film deve essere avvolto a 45 gradi iniziando da una delle estremita'. In questo modo si formera' una spirale con il margine sovrapposto per circa 2 cm.
Una delle persone fa ruotare lentamente il tubo mentre l'altra svolge il rotolo di film facendolo aderire al tessuto impregnato di resina.